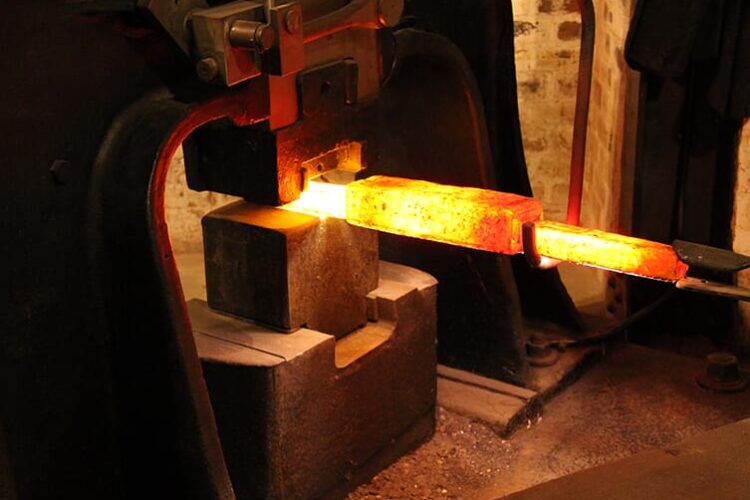
I. Introduction to Forging
II. Benefits of Forging
III. Different Types of Forging Processes
IV. Applications of Forged Products
Welcome, curious reader! Today, we’re diving into the fascinating world of forging. Have you ever wondered how those sturdy metal products are made? Well, forging is the ancient craft that’s been used for centuries to shape metal into various forms. Let’s explore this age-old technique and discover its wonders together.
Imagine a blacksmith, hammer in hand, skillfully shaping a piece of metal into a useful tool or intricate design. That’s the essence of forging – the art of manipulating metal through compressive forces to create strong and durable products. It’s a craft that requires skill, precision, and a deep understanding of metallurgy.
Forging is all about taking raw materials, heating them to high temperatures, and then using various tools to shape them into desired forms. The process involves applying pressure to the metal to deform it, improving its strength and durability in the process. It’s a labor-intensive technique that yields exceptional results.
One of the key aspects of forging is the use of heat. By heating the metal to high temperatures, it becomes more malleable and easier to work with. This allows for intricate designs and precise shaping, resulting in products that are not only strong but also visually appealing.
Whether it’s creating tools, machinery parts, or decorative items, forging is a versatile technique that has been used in various industries. From aerospace and automotive to construction and manufacturing, forged products play a vital role in our everyday lives. The durability and strength of forged products make them ideal for demanding applications where quality and reliability are paramount.
So, the next time you pick up a sturdy tool or admire a beautifully crafted piece of metalwork, remember the art of forging that went into creating it. It’s a centuries-old tradition that continues to thrive, thanks to skilled craftsmen and modern technology working hand in hand.
Forging is an ancient art that has been around for thousands of years. It involves shaping metal through the use of heat and pressure to create strong and durable products. While modern technology has brought about new ways to create metal products, forging still remains a popular method due to its many benefits.
Benefits of Forging
Forging offers a wide range of benefits that make it a preferred method for creating metal products. Here are some of the key advantages:
- Strength: One of the main benefits of forging is the strength of the finished product. By hammering and shaping the metal under high pressure, forging creates a product that is incredibly strong and durable. This makes forged products ideal for high-stress applications where strength is crucial.
- Quality: Because forging involves the manipulation of metal at high temperatures, it helps to eliminate any imperfections in the material. This results in a high-quality finished product that is free from defects and has a consistent grain structure, making it more reliable and long-lasting.
- Customization: Forging allows for a high degree of customization, as the metal can be shaped and formed into complex designs and shapes. This makes it an ideal method for creating unique and specialized products that meet specific requirements.
- Cost-Effective: While forging may require initial investment in equipment and tools, the long-term cost benefits can outweigh the upfront expenses. The strength and durability of forged products mean that they have a longer lifespan, reducing the need for frequent repairs or replacements.
- Environmentally Friendly: Unlike other metal fabrication methods that produce a significant amount of waste and emissions, forging is a more environmentally friendly option. The process generates minimal waste and consumes less energy, making it a sustainable choice for metal production.
Overall, the benefits of forging make it a reliable and efficient method for creating high-quality metal products that meet a wide range of industrial and commercial needs. Whether you are looking for strength, customization, or cost-effectiveness, forging offers numerous advantages that make it a preferred choice for many industries.
“`html
Forging is an ancient art that has been around for thousands of years. It involves shaping metal through the use of heat and pressure to create strong and durable products. While modern technology has brought about new ways to create metal products, forging still remains a popular method due to its many benefits.
Benefits of Forging
Forging offers a wide range of benefits that make it a preferred method for creating metal products. Here are some of the key advantages:
- Strength: One of the main benefits of forging is the strength of the finished product. By hammering and shaping the metal under high pressure, forging creates a product that is incredibly strong and durable. This makes forged products ideal for high-stress applications where strength is crucial.
- Quality: Because forging involves the manipulation of metal at high temperatures, it helps to eliminate any imperfections in the material. This results in a high-quality finished product that is free from defects and has a consistent grain structure, making it more reliable and long-lasting.
- Customization: Forging allows for a high degree of customization, as the metal can be shaped and formed into complex designs and shapes. This makes it an ideal method for creating unique and specialized products that meet specific requirements.
- Cost-Effective: While forging may require initial investment in equipment and tools, the long-term cost benefits can outweigh the upfront expenses. The strength and durability of forged products mean that they have a longer lifespan, reducing the need for frequent repairs or replacements.
- Environmentally Friendly: Unlike other metal fabrication methods that produce a significant amount of waste and emissions, forging is a more environmentally friendly option. The process generates minimal waste and consumes less energy, making it a sustainable choice for metal production.
Overall, the benefits of forging make it a reliable and efficient method for creating high-quality metal products that meet a wide range of industrial and commercial needs. Whether you are looking for strength, customization, or cost-effectiveness, forging offers numerous advantages that make it a preferred choice for many industries.
“`
Different Types of Forging Processes
Forging is a versatile manufacturing process that involves shaping metal through the application of force. There are several different types of forging processes, each with its own unique characteristics and advantages. Let’s take a closer look at some of the most common types of forging:
1. Open-Die Forging
Open-die forging, also known as free forging, is a process where the metal is hammered or pressed into shape between two dies that do not completely enclose the material. This allows for more flexibility in shaping the metal and is often used for producing large, complex parts such as shafts, discs, and rings.
2. Closed-Die Forging
Closed-die forging, also known as impression-die forging, involves shaping the metal between two dies that contain a precut profile of the desired part. This process produces high-precision parts with excellent mechanical properties, making it ideal for creating components with intricate details and tight tolerances.
3. Upset Forging
Upset forging, also known as heading, involves increasing the cross-sectional area of the metal by compressing it axially. This process is commonly used for producing items like bolts, screws, and other fasteners that require a larger diameter at one end.
4. Roll Forging
Roll forging, also known as roll forming, is a process where the metal is shaped by passing it between two rotating rolls. This method is often used for producing long, cylindrical parts like shafts and tubes, as well as complex shapes with consistent dimensions.
5. Swaging
Swaging is a forging process that involves reducing the diameter of a metal rod or tube by forcing it through a die or series of dies. This method is commonly used for producing items like pins, rivets, and bullets, as well as for creating decorative elements with a tapered profile.
6. Isothermal Forging
Isothermal forging is a process where the metal is heated to the same temperature as the dies, allowing for faster and more efficient shaping of the material. This method is often used for producing parts with complex geometries and intricate details, as well as for improving the overall mechanical properties of the finished product.
Each type of forging process has its own unique strengths and applications, so it’s essential to choose the right method based on the specific requirements of your project. Whether you need a high-strength component for a critical application or a custom-designed part with intricate details, forging offers a wide range of options to meet your needs.
“`html
Different Types of Forging Processes
Forging is a versatile manufacturing process that involves shaping metal through the application of force. There are several different types of forging processes, each with its own unique characteristics and advantages. Let’s take a closer look at some of the most common types of forging:
1. Open-Die Forging
Open-die forging, also known as free forging, is a process where the metal is hammered or pressed into shape between two dies that do not completely enclose the material. This allows for more flexibility in shaping the metal and is often used for producing large, complex parts such as shafts, discs, and rings.
2. Closed-Die Forging
Closed-die forging, also known as impression-die forging, involves shaping the metal between two dies that contain a precut profile of the desired part. This process produces high-precision parts with excellent mechanical properties, making it ideal for creating components with intricate details and tight tolerances.
3. Upset Forging
Upset forging, also known as heading, involves increasing the cross-sectional area of the metal by compressing it axially. This process is commonly used for producing items like bolts, screws, and other fasteners that require a larger diameter at one end.
4. Roll Forging
Roll forging, also known as roll forming, is a process where the metal is shaped by passing it between two rotating rolls. This method is often used for producing long, cylindrical parts like shafts and tubes, as well as complex shapes with consistent dimensions.
5. Swaging
Swaging is a forging process that involves reducing the diameter of a metal rod or tube by forcing it through a die or series of dies. This method is commonly used for producing items like pins, rivets, and bullets, as well as for creating decorative elements with a tapered profile.
6. Isothermal Forging
Isothermal forging is a process where the metal is heated to the same temperature as the dies, allowing for faster and more efficient shaping of the material. This method is often used for producing parts with complex geometries and intricate details, as well as for improving the overall mechanical properties of the finished product.
Each type of forging process has its own unique strengths and applications, so it’s essential to choose the right method based on the specific requirements of your project. Whether you need a high-strength component for a critical application or a custom-designed part with intricate details, forging offers a wide range of options to meet your needs.
“`
Applications of Forged Products
Forging is a versatile manufacturing process that has a wide range of applications across various industries. The high strength and durability of forged products make them ideal for demanding applications where performance and reliability are critical. Let’s explore some common applications where forged products are widely used:
1. Automotive Industry
The automotive industry is one of the largest consumers of forged products. Components such as crankshafts, connecting rods, gears, and axles are often made through forging due to the superior strength and fatigue resistance of forged materials. These components play a crucial role in ensuring the performance and safety of vehicles.
2. Aerospace Industry
In the aerospace industry, where safety and reliability are paramount, forged products are extensively used for critical components such as landing gear, engine parts, and structural elements. The high strength-to-weight ratio of forged materials makes them ideal for aerospace applications, where weight savings are crucial for fuel efficiency.
3. Oil and Gas Industry
The oil and gas industry relies on forged products for various components used in drilling, extraction, and processing operations. Forged materials are preferred for their resistance to high pressure, corrosion, and extreme temperatures, making them well-suited for challenging environments in the oil and gas sector.
4. Power Generation
In the power generation sector, forged products are used in turbines, generators, and other critical equipment where high strength and reliability are essential. Forged components help improve efficiency, reduce maintenance costs, and enhance overall performance in power plants and energy production facilities.
5. Defense and Military Applications
Forged products also play a crucial role in defense and military applications, where reliability and performance under extreme conditions are vital. Components such as armor plating, artillery shells, and weapon parts are often forged to meet stringent requirements for strength, durability, and precision.
Overall, the applications of forged products are diverse and widespread, ranging from heavy machinery and construction equipment to hand tools and consumer goods. Whether it’s enhancing performance in automotive engines or ensuring safety in aerospace systems, forged products continue to be a vital part of modern manufacturing across various industries.
“`html
Applications of Forged Products
Forging is a versatile manufacturing process that has a wide range of applications across various industries. The high strength and durability of forged products make them ideal for demanding applications where performance and reliability are critical. Let’s explore some common applications where forged products are widely used:
1. Automotive Industry
The automotive industry is one of the largest consumers of forged products. Components such as crankshafts, connecting rods, gears, and axles are often made through forging due to the superior strength and fatigue resistance of forged materials. These components play a crucial role in ensuring the performance and safety of vehicles.
2. Aerospace Industry
In the aerospace industry, where safety and reliability are paramount, forged products are extensively used for critical components such as landing gear, engine parts, and structural elements. The high strength-to-weight ratio of forged materials makes them ideal for aerospace applications, where weight savings are crucial for fuel efficiency.
3. Oil and Gas Industry
The oil and gas industry relies on forged products for various components used in drilling, extraction, and processing operations. Forged materials are preferred for their resistance to high pressure, corrosion, and extreme temperatures, making them well-suited for challenging environments in the oil and gas sector.
4. Power Generation
In the power generation sector, forged products are used in turbines, generators, and other critical equipment where high strength and reliability are essential. Forged components help improve efficiency, reduce maintenance costs, and enhance overall performance in power plants and energy production facilities.
5. Defense and Military Applications
Forged products also play a crucial role in defense and military applications, where reliability and performance under extreme conditions are vital. Components such as armor plating, artillery shells, and weapon parts are often forged to meet stringent requirements for strength, durability, and precision.
Overall, the applications of forged products are diverse and widespread, ranging from heavy machinery and construction equipment to hand tools and consumer goods. Whether it’s enhancing performance in automotive engines or ensuring safety in aerospace systems, forged products continue to be a vital part of modern manufacturing across various industries.
“`
Comments